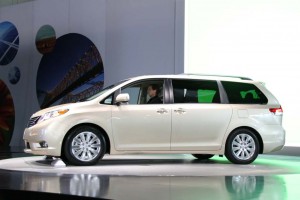
With the launch of U.S. production, the 2011 Toyota Sienna is taking aim at the minivan's segment leaders, Chrysler and Hona.
Production of the all-new 2011 Toyota Sienna minivan has begun at the automaker’s assembly plant, in Princeton, Indiana. Unveiled at the Los Angeles Auto Show, last November, and garnering strongly favorable reviews since then, the new minivan is taking aim at the people mover segment’s two top performers, Honda and Chrysler.
Hoping to gain a better grip on the American market, Sienna was styled at Toyota’s Calty Design Research Center in Newport Beach, Calif., with engineering duties handed over to the Toyota Technical Center in Ann Arbor, Mich.
Production of the new Sienna — as well as that of the Highlander SUV, which began last October – comes as welcome news for the Indiana plant, which has been underutilized during the current economic downturn.
TMMI reached a critical crossroads in mid-2008 when Toyota faced significant overcapacity in North America. As a partial solution, the automaker consolidated production of the Tundra full-size pickup – originally built at TMMI – into its new truck plant, in San Antonio, Texas.
Other shifts left the Princeton plant running well below capacity – something Toyota normally doesn’t tolerate. But the automaker decided to keep its 4,200 workers on the payroll while it sorted things out and got the plant ready for the new Highlander and Sienna models.
“Without a doubt, our team members were worried. The plant faced an uncertain future when the banking and housing crisis brought the economy to its knees and the auto industry with it,” said Will James, senior vice president of Toyota Motor Manufacturing, Inc., or TMMI. “Layoffs were happening all over the auto industry. It would be many months before Highlander production began. As a result, half of our team members were not building vehicles.”
Fixing this problem was important not only to Toyota and its suppliers, who employ thousands of people in Indiana and many other states, Toyota officials
Toyota has now invested approximately $450 million to upgrade the plant. With the start of Highlander production, last October, and the recent launch of the all-new Sienna, the plant’s outlook has improved dramatically.
TMMI’s survival story is rooted in the way it treated team members during the downturn, an approach far different from most manufacturers. General Motors and Chrysler each had programs in place to keep idled workers on the payroll. But at the insistence of conservative Congressman and Senators — including several from states where Toyota is an important employer — the so-called Jobs Bank programs were dismantled when the two automakers each sought federal aid, last year,
Though it avoided a federal bailout, Ford Motor Co. also dismantled its costly Jobs Bank program, which dated back to the.
While Toyota doesn’t have a formal program of its own, “It made more sense to further invest in our experienced team members,” the carmaker’s James said. “We refocused our work. When we weren’t building vehicles, we were preparing for a brighter future.”
TMMI implemented a training program to give workers a deeper understanding of the Toyota Production System and enhance their manufacturing skills.
“It’s difficult to roll out such comprehensive training when the line is moving,” James said. “Our company spent a lot of time developing the best way to do every job in the plant, so the downturn was actually a great opportunity to complete this training in order to sharpen our skills.”
Other team member ideas bolstered safety, ergonomics and ensured consistent quality. For example, the installation of the lower front console on the all-new Sienna put the team member in an awkward position. Team members found a small power tool that ensured the console snapped securely in place every time while eliminating an ergonomic issue.
“Our team members know better than anyone else how to do their jobs and they always have the flexibility to change processes in order to improve safety, quality and efficiency,” James said.