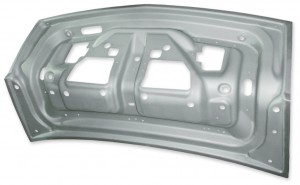
General Motors is testing an industry-first thermal-forming process and proprietary corrosion resistance treatment for lightweight magnesium sheet metal.
General Motors is testing a new thermal-forming process and its own corrosion-resistance treatment for magnesium to as an alternative to steel and aluminum for vehicle body panels.
Eventually, GM wants to license the technology to suppliers to provide significant amounts of magnesium sheet to trim weight from its vehicles.
Automakers are under pressure to increase fuel economy and one to do that is reduce weight. Magnesium could help.
The problem is magnesium is more difficult to form into complex shapes and it’s expensive.
But the foray into magnesium shows how far automakers will go in their efforts to reduce weight.
Magnesium weighs 33 percent less than aluminum and 75 percent less than steel, which could provide significant weight savings.
Automakers have struggled to make reliably strong and non-corroding magnesium sheet metal panels using traditional panel forming methods. GM’s patented process turns up the heat on magnesium to 842 degrees Fahrenheit, allowing the material to be molded into precise, rigid shapes.
Using this process, GM developed a production-ready magnesium rear deck lid inner panel that withstood 77,000 robotic slams and 250-kilogram impact drops without any issues.
Die-cast magnesium has been used in a variety of parts ranging from steering wheels to engine cradles, but GM said it is the first to use thermal-formed magnesium sheet metal in structural applications, and it expects magnesium sheet applications to grow with additional materials and process improvements targeted at reducing cost.
“This innovative use of magnesium is just one example of how GM is leveraging breakthrough technologies that will benefit our customers around the globe,” said Jon Lauckner, GM chief technology officer and vice president of Global Research & Development. “Using high-strength lightweight materials such as magnesium and aluminum is one of the most effective ways to improve vehicle fuel economy and driving performance.”
GM is not the first automaker to use magnesium in a body panel. The 2010 Lincoln MKT introduced a tailgate has a cast magnesium inner panel with a stamped aluminum skin, saving 22 pounds over a comparable steel piece.
This type of combination of materials could be the key to lightweighting vehicles, according to Jay Baron, chairman of the Center for Automotive Research. Baron, who has a strong interest in lightweight materials told TheDetroitBureau.com that he is interested in helping suppliers of various materials work together to combine materials to take advantage of each material’s strengths.
Click here to read more about vehicle lightweighting.
The United States Automotive Materials Partnership estimates that by 2020, 350 pounds of magnesium will replace 500 pounds of steel and 130 pounds of aluminum per vehicle, an overall weight reduction of 15 percent. This weight savings would lead to a fuel savings of 9 percent to 12 percent.
But the high-tech material is pricey, costing about five times the price of steel and 20 percent more than aluminum, according to www.steelonthenet.com.
GM will conduct a test run of 50 vehicles to be bought by consumers in the fourth quarter, but the automaker would not indicate the model or models that will test the expanded use of magnesium, Automotive News reported.
The rear deck lid inner panel, reduces weight by 2.2 pounds compared to a steel deck lid inner panel.
“Every gram of weight reduction matters when it comes to improving fuel economy,” said Greg Warden, GM executive director for global vehicle body engineering. “Being able to replace heavier metals with one of the lightest will help us deliver better fuel economy to customers around the world while also still providing the safety and durability they expect.”
Automakers also have struggled to make magnesium corrosion resistant. GM’s proprietary treatment for thermal-formed magnesium resisted 10 consecutive weeks of 24-hour environmental tests involving salt spray, 100 percent humidity and extreme temperatures.
“Like all of our advanced material vehicle parts, we subjected the magnesium trunk lid to the most severe strength and corrosion tests we know of, and it passed with flying colors,” said Jon Carter, GM R&D metals researcher. “We expect it to perform extremely well even in the harshest environments.”