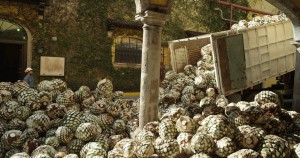
Partnering with tequila maker Jose Cuervo, Ford takes what's left of these agave plants and turns them in to bioplastic-based components.
One tequila, two tequila, three tequila … Ford?
The Dearborn, Michigan-based automaker is teaming with Jose Cuervo to develop a new bioplastic that will be used for a variety of applications in new cars, saving the maker money and weight and lowering energy consumption.
The byproduct of the agave plants harvested to make tequila will be used in vehicle interior and exterior components, such as wiring harnesses, HVAC units and storage bins. Initial assessments suggest the material holds great promise due to its durability and aesthetic qualities.
“At Ford, we aim to reduce our impact on the environment,” said Debbie Mielewski, Ford senior technical leader, sustainability research department.
“As a leader in the sustainability space, we are developing new technologies to efficiently employ discarded materials and fibers, while potentially reducing the use of petrochemicals and light-weighting our vehicles for desired fuel economy.”
(Dandelion tires and wires from soy. To find out more about automotive recycling, Click Here.)
The growth cycle of the agave plant is a minimum seven-year process. Once harvested, the heart of the plant is roasted, before grinding and extracting its juices for distillation. Jose Cuervo uses a portion of the remaining agave fibers as compost for its farms, and local artisans make crafts and agave paper from the remnants.
Ford using the leftovers from a plant in the manufacture of a vehicle isn’t unusual. The company uses eight different “waste” products as recycled materials in vehicles, including soy foam, castor oil, wheat straw, kenaf fiber, cellulose, wood, coconut fiber and rice hulls.
Here’s the breakdown:
- Old denim and T-shirts become interior padding and sound insulation in most Fords.
- Tomato skins are used in wiring brackets and storage bins.
- Recycled plastic bottles become carpeting, wheel liners and shields in Transit and C-Max.
- Old tires are used in seals and gaskets.
- Rice hulls reinforce plastic in F-150 electrical harnesses.
- Soy-based foams are used as seat cushions, seat backs and head restraints.
- Wheat straw reinforces storage bins in Flex.
According to the United Nations Environment Program, 5 billion metric tons of agricultural biomass waste is produced annually. A byproduct of agriculture, the supply of materials is abundant and often underutilized. Yet the materials can be relatively low cost, and can help manufacturers to offset the use of glass fibers and talc for more sustainable, lightweight products.
(Dutch company wants to turn plastic waste into roads. Click Hereto see how.)
“There are about 400 pounds of plastic on a typical car,” said Mielewski. “Our job is to find the right place for a green composite like this to help our impact on the planet. It is work that I’m really proud of, and it could have broad impact across numerous industries.”
Ford isn’t alone, other makers have been using different recycled materials for many years. In fact, Honda had to recall thousands of vehicles that had soy-based wire covers because the green products attracted rodents that ate through the covers, damaging the wires underneath.
Suppliers are in on the act too. Continental Tire recently unveiled its new tire made from, in part, dandelions. The German supplier hopes to put the synthetic material, known as taraxa gum, into production “in five to 10 years” as an alternative to conventional rubber tire treads.
(Automakers rack up awards for their newest green machines. Click Here for more.)
The dandelion is actually just one of perhaps 1,200 different types of plants from which a similar latex polymer could be derived. One advantage is that it takes seven years to grow a rubber tree to the point where it can be tapped for sap. A crop of Russian dandelions – the best type for synthetic rubber — is ready in less than a year.