Just over three years ago, I attended the ground breaking ceremony for the new Kia factory in West Point, Georgia. The weather was soggy and damp and there wasn’t much to see beyond a hilly, 2,100- acre site that the Korean automakers promised to turn into one of North America’s assembly plant – a heck of a stretch for a company long known for building econocars using cheap labor.
But just a few weeks ago, as I turned off the specially constructed exit ramp and turned onto Kia Avenue, I had another chance to visit the site where my first glimpse revealed an ultra modern, pristine automotive manufacturing campus gleaming in the warm sun. Three years had brought changes. Major changes.
The factory was finished, the production line running, stamping presses installed, welding operations opened, paint shop ready and training of first employees had been completed. The new, $1 billion factory was warming-up the production line to produce the new, 2010 Kia Sorento crossover vehicle. Since my latest trip to Georgia, the facility has gone from prototypes to market-ready versions of the Sorento
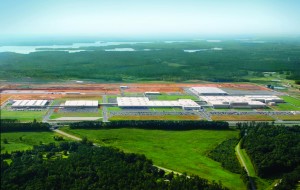
Though the new Kia plant in Georgia cost more than $1 billion, state and local incentives covered a large share of that price tag.
Though virtually every serious player in the U.S. market now operates at least one “transplant” assembly line here, Kia’s commitment required significant cooperation from state, national, regional and community involvement, investment and participation. There were millions offered in the form of tax abatements, fully paid services and other incentives. State investment alone was about $165 million, which includes $34.6 million for the site and another $48.5 million to prepare the 650-acre “pad” for the plant. Various tax abatements kicked in another $130 million.
But another plus was getting help signing up a well-trained, non-organized workforce with wages that are, on balance, similar to those paid at factories in Korea – and without the aggressive, contentious and combative unions that often make manufacturing in the small nation so difficult.
Automobile assembly plants are among the most sought after manufacturing operations, both in emerging and established nations, because they bring significant employment and good wages to often depressed areas.
The location of the Kia factory in West Point, Georgia reflects the fact that this one-time home factories and mills producing cloth and woven fabrics had fallen on hard economic times for residents and businesses. The Kia factory was its only hope.
When fully operational, Kia promises the plant will provide jobs for over 2,500 workers in the economically distressed region while on-site and nearby suppliers – many of them transplant Korean companies — will create 7,500 additional jobs in the region.
When the Kia factory was first announced, a staggering 43,013 job applications were received via the Internet in just one month, a record-setting number according to Georgia Quick-Start, Kia’s training partner. Seventy-five percent of the applicants were from Georgia, 97% had a high school education or equivalent and nearly 30% had completed a two or four-year college program.
Training was a critical element in the planning and development of the new factory, thus the first structure on the site was a $14 million, 70,000 square-foot training center constructed, staffed and paid for by the state of Georgia. Applications were extensively prescreened and reviewed by Kia and the Georgia Department of Labor, and after a long process, those who made the initial cut still had to go through 40 hours of pre-employment assessment — without compensation of any kind.
After each new worker is hired there is an additional 80 hours of orientation and core skills training. The hands-on training sessions I watched, combine education with simultaneous testing, all observed and graded by instructors working with handheld computer devices which input grades for each trainee. “Training,” noted the tour guide, “Is an on-going process … it never ends.” One unexpected experience for over 800 of the first 1,250 new Team Members was a two-week trip to Korea for further job and skills training.
The wages paid to workers at the new factory range from $14 to $20 per hour. Using a median of $17 per hour, that works out to $ 2,720.00 per month. That’s significantly less than the typical Big Three Detroit worker and only about $180 more than the $2,540 (in U.S. dollars) paid to the average Korean factory worker, according to the National Statistics Office of Korea. (And that’s a national average. Korean autoworkers are, as they’ve long been here, some of the country’s manufacturing elite.)
The relatively low wages, the West Point factory’s high level of automation and the potentially harmonious labor relations Kia built into the hiring process could all offset any slight remaining labor cost advantage that would remain from producing cars back in Korea. And that doesn’t even account for sharply reduced shipping costs and the advantages of being able to better link production to shifts in market conditions – something difficult to achieve when your supply lines stretch all the way across the Pacific.
Notably, Kia went all-in with West Point, the factory complex including not just the assembly line but a body stamping facility, paint shop, welding facility, various parts depots and, significantly, a transmission shop where Sorento’s six-speed automatic transmission is produced. There’s also a two mile test track.
The hefty incentives may have helped, but Kia is still betting a large sum on the new West Point plant. If it pays off, the company could be better positioned to achieve its ambitious growth targets. If it fails, it could be stuck with significant capacity it won’t need – and some hefty bills.
On the local front, Georgia’s state and local governments have tossed plenty of their own money into the pot and could face a serious voter backlash, if the project fails, considering current economic conditions.
“Predicting the future is always difficult,” acknowledged George Ewing, the head of the State of Georgia Economic Development Authority, but he confidently predicted that “with Kia’s sales growth in the U.S., the investment by the entities participating in the new factory will have a more than a satisfactory ROI.”