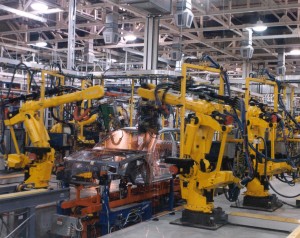
Will demand for better wages hurt the Chinese auto industry? A rise in the value of the Remnimbi could be the real problem.
Toyota has again suspended production at its main Chinese assembly plant in the wake of a walkout by workers at a key supplier facility. The second strike in a month at a joint venture partially owned by Japanese partsmaker Denso, hits hard a Toyota facility with the capacity for 360,000 vehicles a year.
The walkout comes in the wake of similar strife at a Honda transmission plant in China that cost that maker thousands of units of production and eventually led Honda to approve significant increases in wages and benefits to get angry workers back onto the line.
These and other recent labor confrontations come as a surprise to China-watchers who know how much emphasis the Beijing government puts on maintaining the appearance of social order. And they’re all the more unusual considering the traditionally company-friendly approach unions have played in China.
Complicating matters is the reluctant decision by government leaders to accept American demands to let the Remnimbi, rise to reflect the real-world value of the nation’s currency. While Beijing has tried to assuage nervous Chinese who fear the currency move might have a negative impact on exports – and thus jobs – there’s a growing sense of concern that the era of cheap Chinese products may be coming to an end. The question is whether the vast Asian nation can remain competitive.
Even though standards of living have been on the rise, in much of China, factories typically pay less than $1,000 a month, and sometime barely more than $100. At the Honda factory, employees only agreed to go back to work when the company approved substantial improvements in the $230 a month base wage – a figure kept low through the use of “interns” from schools in the surrounding communities.
But one only has to look to bigger cities, like Shanghai and Beijing, where upward pressure on pay has become the norm for several years, and where workers at major auto plants often now earn several thousand a month, and have been steadily pressing for more.
That’s encouraged some existing automakers to migrate to smaller cities and more rural parts of the country, but the Honda and Denso strikes show that strategy may no longer be working as well as it did just a few years ago.
How much strike fever will spread is uncertain. Traditionally, the central communist government has not tolerated public protests of any form, but they may be unwilling to seem overly aggressive in suppressing what some observers feel is widespread and growing frustration with low wages and often difficult working conditions. Worldwide attention has been focused on a major Chinese electronics manufacturer – whose clients include America’s Apple – where over-worked and overstressed employees have been committing suicide at an alarming rate.
One way or the other, though, higher labor costs seem a certainty. In the automotive industry, the impact might prove moderate. Even in the U.S., labor accounts for only about 11% of the total cost of the average automobile. In China, it’s a fraction of that figure, even though the country’s plants are far less automated.
“They’ll learn to adapt, as we did,” suggests Euisun Chung, vice chairman of South Korea’s Hyundai Motor Co.
When Hyundai and its national rivals first burst onto the global automotive scene, in the mid-1980s, they had a huge cost advantage over U.S., European and Japanese automakers. But constant – and often violent – strikes rapidly drove up wages and benefits and, by the mid-1990s, labor costs reach near-parity with what British autoworkers made, according to Korean government data.
That led Hyundai and other Korean carmakers to take dramatic steps to improve productivity. Indeed, that approach made it possible for both Hyundai and its sibling Kia brand to set up assembly plants in the U.S. Highly-automated, they are among the most efficient in North America and are at little cost disadvantage to factories back home.
“We’ll either see the (Chinese) government try to put down” the movement for higher wages, “or embrace it and adopt,” concurs George Peterson, head of the U.S. consulting firm, AutoPacific, Inc.
There’s plenty of room to improve productivity at most Chinese plants, Peterson pointed out. When General Motors set up its first joint venture assembly line, in Shanghai, a decade ago, it installed only a couple robots. And they were used primarily to handle jobs humans had difficulty with, like applying sealant to windshields, rather than to reduce manpower.
As labor rates have risen, factories like Shanghai-GM, or SGM, have already begun to automate more heavily, and that trend is likely to gain momentum.
As for the currency shift, that could be more problematic, said the analyst. “If they float it,” rather than force a gradual rise in the Remnimbi’s value, “all bests are off.”
At least that would be the case for China-based auto suppliers, who are increasingly serving export markets. Carmaker like S-GM, and homegrown brands, such as Geely and Chery, might feel less of an impact because the Chinese market has been growing so fast most of the country’s auto production capacity has been earmarked for domestic demand.
But there’s been growing interest in exporting, especially by Chinese automakers like BYD, which has promised to enter the American market in the next several years. A sharp rise in prices could delay or completely abort its plans.
And if China’s vast export machine slows, costing jobs, that could stunt the nation’s fast-growing economy, observers warn. In turn, that might slow down the Chinese auto market, which continued to grow at high double-digit rates even as the rest of the world’s demand for new cars fell to Depression-era levels over the last several years.
it is hitting electronics too.
http://news.bbc.co.uk/2/hi/business/10294850.stm