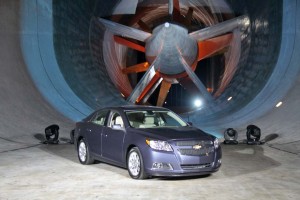
A 2013 Chevy Malibu prototype sits in the business end of the GM wind tunnel, the massive blades able to blast wind at speeds up to 138 mph.
The smokescreen flows smoothly up and over the hood, the stream arcing gracefully over the roof. But, when it hits the mirror it shatters into eddys and curls. Who knew something so small could cause so much trouble.
Actually, it’s something John Cafaro was well aware when he set to work on the 2013 Chevrolet Malibu. It’s often the most subtle details that can cause the most serious problems when it comes to designing a car that cuts through the wind like a knife.
Aerodynamics have played a critical role in aircraft development almost since the Wright Brothers’ Flyer first took to the air. But it would be decades before automotive stylists truly understood the role the concept could play in their designs – helping improve performance and vehicle stability while also yielding significant improvements in fuel economy.
Today, however, any good designer “has aerodynamic solutions in mind” the moment they begin work on a new project, explains Cafaro, the veteran GM designer, as he leads a tour of the automaker’s mammoth wind tunnel at its sprawling technical center in the Detroit suburb of Warren, Michigan.
The heart of the donut-shaped facility is a massive fan, its spruce blades sweeping a circle 43 feet in diameter. Driven by a 4200-horsepower electric motor, it can creates a continuous flow of air that blasts through a specially designed test chamber at speeds reaching 138 mph – more than matching the peak gales seen during Hurricane Irene, last week.
The chamber is equipped with a special pad whose delicate sensors can be positioned under the wheels of anything from a small scale model to a full-size pickup truck. “They’re sensitive enough we could a quarter on the corner of a pickup and the scales would see it,” explains Suzy Cody, an aerodynamic development engineer.
The data those scales produce can reveal a variety of things to a trained engineer. Wind drag, for one thing, lift, and downforce.
The latter two forces are particularly important at higher speeds – and essential in motor sports. While you want an airplane to get lift as it gains speed, an automobile should actually hunker down to stay in contact with the road, which improves its ability to steer and negotiate curves and uneven terrain.
But drag is the real issue. Too much of it is, well, really a drag, as it can dramatically reduce performance and fuel economy at the same time.
With the next-generation Malibu, Cafaro notes, a variety of steps have been taken to reach a coefficient of drag of 0.29 – equal to some of the world’s best sports cars. That’s not easy when you’re working on a big sedan, rather than a sleek, low-slung 2-seater.
Some of the solutions are simple: the bumpers and front fenders are carefully rounded to ensure air “stays attached and flows down the side of the car as closely to the body as possible,” says John Bednarchik, the lead aerodynamic researcher on the Malibu program. The rear fenders, however, are sharp-edged so the air flow breaks cleanly away.
The new Malibu will adopt several new features to improve air flow around one of the most troubling areas of the vehicle: the grille. Electrically-controlled shutters seal off the engine compartment when the motor is running at optimum temperature, reducing turbulence under the hood. Meanwhile, underbody panels reduce turbulence beneath the car, says Cafaro.
Mirrors present designers with another headache, he adds. You want them big for good visibility, but the larger they are the more drag they create and that, in turn, results in wind noise passengers hear. So, with the 2013 Malibu, the U.S. version will opt for slightly smaller side mirrors optimized to limit wind resistance and noise.
Sometimes an unforeseen problem in one part of a design can create challenges on another part of the vehicle. Or vice versa. The new Nissan Leaf’s blister-like headlamps may look a bit ungainly but they gently nudge the airflow outward and away from the battery car’s mirrors, reducing both drag and noise. That’s the sort of complex solution that is becoming more common as automakers struggle to find every possible way to improve aerodynamics.
In decades past, designers spent a significant amount of time in the wind tunnel studying the data and watching smoke patterns. These days, says Cody, computer modeling is becoming so good that much of the initial design work can be done online. Nonetheless, she adds, there are so many vehicles in the GM line-up that need be optimized that the wind tunnel is in use almost 24 hours a day, often seven days a week.
But there are other tools that help improve the facility’s efficiency. In a warren of rooms hidden underneath the GM design center a laser light bounces across the surface of a clear liquid. Over the next few hours a plastic version of an alternate taillight cover will emerge from the brew.
Using this technique, called rapid prototyping, designers can quickly test a variety of solutions to see which one is most effective. Once the data confirm it production tools can be prepared, slowly leading up to the day when the new, streamlined 2013 Chevrolet Malibu begins rolling down the assembly line.