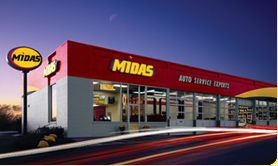
No longer is the EPA just pursuing large and flagrant violators such as General Electric.
If you have ever wondered why a “disposal fee” is increasingly tacked on to your auto repair bill, all you have to do is look at the enforcement the Environmental Protection Agency is doing against businesses that flout the law and endanger public safety. No longer is the EPA just pursuing large and flagrant violators such as General Electric, but it is now stepping up monitoring of smaller businesses that TDB readers deal with.
The latest such example occurred in Bellevue, Washington, where a Midas Muffler shop has reached a $9,300 settlement with the Environmental Protection Agency (EPA) to resolve alleged, violations of the federal Toxic Substances Control Act (TSCA) related to the mishandling of PCBs.
The PCB problem was initially discovered by an oil recycling company in Seattle, who received a shipment of 150 gallons of used oil from Midas in Oct. 2007. Midas did not inform the recycler that the used oil contained PCBs. When the recycler tested the oil and found that it was contaminated with PCBs, they notified EPA. The company was forced to dispose all of the used oil as PCB-contaminated fluid.
According to Daniel Duncan, EPA’s regional PCB program coordinator in Seattle, facilities that handle used oil that may contain PCBs need to have proper testing, notification, storage, shipping, and disposal practices and follow their obligations under TSCA.
“These federal rules are intended to protect human health and the environment from risks posed by these toxic chemicals,” said Duncan. “This is why it’s so important for companies to comply with federal regulations, especially here where PCBs and other persistent toxic chemicals pose a threat to Puget Sound. If they don’t, they put people and the environment at risk, and they face potential fines for noncompliance.”
Midas’ alleged violations included:
- Failure to properly mark the contaminated oil container with a PCB label;
- Failure to notify EPA in advance of the shipment of the PCB waste;
- Failure to prepare a manifest for the shipment of the PCB waste.
Companies should use either a field screening test kit or send a sample of their used oil to a laboratory for analysis to determine if it contains PCBs. It’s important for companies to make this determination before sending the used oil for energy recovery/disposal. If the used oil is found to have PCBs the company must isolate the PCB containing oil from further contaminating other used oil.
Concerns about the toxicity and persistence of PCBs in the environment prompted Congress in 1976 to enact prohibitions on the manufacture, processing and distribution in commerce of PCBs, including “cradle to grave” (i.e. from manufacture to disposal) management of PCBs.
EPA Release:
Fort Edward, NY 05/15/2009 The long awaited and historic dredging of the Upper Hudson River to remove PCB-contaminated sediment began today near Roger’s Island in Fort Edward, NY. The start of the first phase of the six-year dredging project, which is being conducted under an agreement with the General Electric Company, was marked today by officials from the U.S. Environmental Protection Agency (EPA) and New York State, elected representatives, and a broad group of community representatives and environmental stakeholders at a river’s edge ceremony in Fort Edward.
“The start of Hudson River dredging is a symbol of victory for the environment and for its river communities,” said George Pavlou, Acting EPA Regional Administrator. “Dredging will help restore the health of the river, and will one day allow people to eat fish that are caught between Fort Edward and Albany. This is an historic day for an historic river.”
“This is another chapter in the story of a river coming back from the brink,” Governor David A. Paterson said. “Forty years ago, the Hudson River was a poster child for pollution, mocked as an open sewer. But through the Clean Water Act, the upgrade of wastewater treatment plants and increased public vigilance fostered by the growing public interest in environmental protection, the Hudson has steadily improved and it is cleaner than it has been in decades. Today, we mark another step forward in the reclaiming of this river for the people and communities of New York.”
The dredging and related work will be conducted by GE under the terms of a November 2006 consent decree. EPA will oversee all aspects of the work; dredging will continue through October 2009, weather permitting. At the conclusion of this first phase of the project, an independent panel of experts will review the results of the dredging and potentially make recommendations for changes that may be incorporated throughout the remainder of the dredging, which is targeted for completion in 2015.
This first phase of the dredging project will be conducted 24 hours a day, six days a week and targets the removal of 265,000 cubic yards of sediment and 20,300 kilograms of PCBs from a six-mile stretch of the river between Roger’s Island and Thompson Island. Sediment removed from the river will be carried by barge to a dewatering facility located on the Champlain Canal in Fort Edward. At this facility, water will be squeezed from the sediment and treated to drinking water standards before being returned to the canal. The remaining PCB-laden dirt will be loaded onto railcars for ultimate disposal at a permitted landfill facility in Andrews, Texas. The entire project will remove an estimated 1.8 million cubic yards of sediment and 113,000 kg of PCBs.
“We have come such a long way over the more than 25-year life of this project, and we could not have reached this day without the participation of literally thousands of people who care about the Hudson River and its legacy,” Pavlou added.
Information about the Hudson River PCBs Superfund site can be found at: http://www.epa.gov/hudson