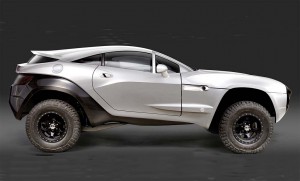
Local Motors debuted its Rally Fighter car at the SEMA show. The car was produced entirely using a 3D printer.
It’s not quite StarTrek, but 3D printing technology comes close, allowing you to turn a digital image into a solid object, everything from toys to tools – and now, even a car.
Phoenix-based Local Motors offered a hint of what it has in mind when it revealed a rough version of its concept at the SEMA Show, promising to put its new printed cars on sale next year for prices ranging from $18,000 to $30,000.
And to underscore the flexibility of its approach, it launched the ModMen Challenge, asking hot rodders, performance fans and the aftermarket community to “hack up” its design to show what they would do. The top 12 will be given cars to bring to life before a final winner is chosen in time for next year’s Specialty Equipment Marketers Association convention in Las Vegas.
“When SEMA approached Local Motors and asked us to 3D print a car at their annual conference, we accepted the challenge with great excitement,” said John “Jay” Roger, Jr., co-founder and CEO of Local Motors. “The hot rod and aftermarket automotive community has always been on the cutting edge of vehicle innovation and we’re thrilled to display the future of car making to this group.”
At its most basic, a 3D printer uses a laser to turn a variety of raw materials – such as plastic or even titanium powder – into a solid object, one pixel at a time, based on the data from a digital file. Simple units are now available for $1,000 or so at local computer stores.
Local Motors’ systems is significantly larger and more complex, but the basic functionality is the same. It uses carbon fiber-reinforced plastic to make most of the vehicle, a process that takes it about 40 hours – which means it isn’t about to aim for a mass market.
After printing out the body, chassis and much of the interior it assembles the remaining components, including the suspension, wheels and tires, and the powertrain. All told, said Roger, its vehicles consist of just 50 components, rather than the thousands used in a conventional vehicle.
But one of the more intriguing aspects to the concept is that the digital files allow for incredible flexibility. Want a bigger vehicle, “click a button.” Want to put a bulge in the hood to make it look more macho? That’s not much more difficult.
(Scion goes heavy metal at SEMA. For more, Click Here.)
Local Motors still has to crash test its planned vehicles to ensure they meet federal safety requirements, but most of those tests will initially be performed in a virtual manner so only a limited number of real models will need to be wrecked.
(Click Here for details about you could share parts with F1 cars.)
That’s not out of line with the way the traditional auto industry works today. Most designs are created in digital form, and virtual testing is the norm. The big difference is that a company like Ford or Toyota ultimately transforms digital data into hard tooling then used to stamp out metal body panels in conventional form, then welds, glues and bolts the parts together to make a car.
(To see why NHTSA is investigating 400,000 Hondas and Infinitis, Click Here.)
Local Motors actually printed one of its cars for the SEMA Show, and it revealed that the process isn’t quite as simple as hooking a computer up to its printer. It took 44 hours to transform the digital file into the actual components. But the company then had to mill the rough parts into finished pieces, something known as subtractive manufacturing, adding another eight hours to the process. The final step was to put everything together, as much like creating a Lego car as building a traditional automobile.
A ready-to-drive car was set to go as the annual SEMA Show wrapped up over the weekend.
Well this is better than people printing guns…